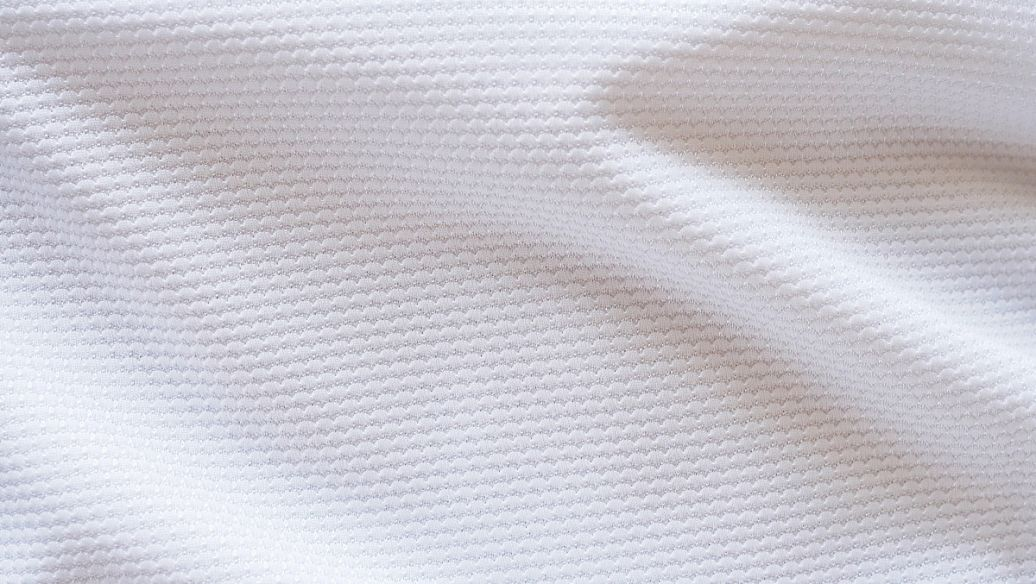
Astarlı parça istehsalı prosesində qüsurların görünüşü qaçılmazdır. Qüsurları necə tez müəyyən etmək və qüsurların növlərini və ölçülərini necə ayırd etmək paltar astarının keyfiyyətini qiymətləndirmək üçün çox vacibdir.
Paltar astarlı parçanın ümumi qüsurları
Xətti qüsurlar
Xətt qüsurları, həmçinin xətt qüsurları olaraq bilinir, uzununa və ya eninə istiqamətlər boyunca uzanan və eni 0,3 sm-dən çox olmayan qüsurlardır. Bu, çox vaxt ipliyin qeyri-bərabər qalınlığı, zəif bükülmə, qeyri-bərabər toxuculuq gərginliyi və avadanlıqların düzgün tənzimlənməməsi kimi iplik keyfiyyəti və toxuculuq texnologiyası ilə əlaqədardır.
Şerit qüsurları
Zolaq qüsurları, həmçinin zolaq qüsurları kimi tanınan, uzununa və ya eninə istiqamətlər boyunca uzanan və eni 0,3 sm-dən çox olan qüsurlardır (bloklu qüsurlar da daxil olmaqla). Bu, çox vaxt iplik keyfiyyəti və dəzgah parametrlərinin düzgün təyin edilməməsi kimi amillərlə bağlıdır.
Zədələnmək
Zərər dedikdə, iki və ya daha çox ipin və ya 0,2 sm2 və ya daha çox iplik və ya çuxurun qırılması və arğacın (uzununa və eninə) istiqamətdə qırılması, kənardan 2 sm və ya daha çox qırılan kənarlar və 0,3 sm və ya daha çox atılan çiçəklər aiddir. Zərərlərin səbəbləri müxtəlifdir, çox vaxt ipliyin qeyri-kafi möhkəmliyi, çözgü və ya arğac ipliklərində həddindən artıq gərginlik, ipliyin aşınması, dəzgahın nasazlığı və düzgün işləməməsi ilə bağlıdır.
Əsas parçadakı qüsurlar
Əsas parçadakı qüsurlar, həmçinin əsas parçadakı qüsurlar, paltar astarlı parça istehsal prosesində baş verən qüsurlardır.
Filmin köpüklənməsi
Film Blistering kimi də tanınan Film Blistering, filmin substrata möhkəm yapışmadığı və nəticədə qabarcıqların meydana gəlməsinə səbəb olan bir qüsurdur.
Yanan
Qurutma sızdırmazlığı astarlı parçanın səthində uzun müddət yüksək temperaturun təsiri ilə yanmış sarı və sərt teksturaya malik olan qüsurdur.
Sərtləşdirmək
Sərtləşmə, digər adı ilə sərtləşmə, astarlı parçanın sıxıldıqdan sonra orijinal vəziyyətinə qayıda bilməməsi və toxumasını sərtləşdirə bilməməsi deməkdir.
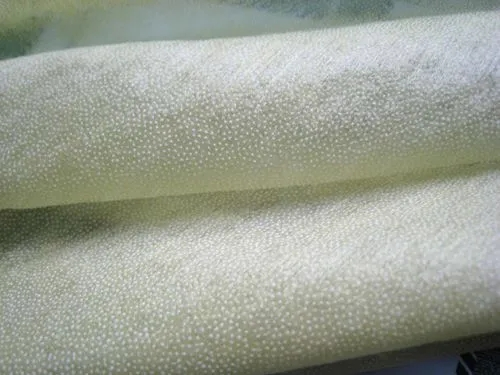
Toz sızması və sızma nöqtələri
Çatışmayan örtük, həmçinin toz sızması kimi tanınır, yapışqan astarının yerli yerində isti əriyən yapışan nöqtə növü parçanın dibinə keçməməsi və dibi açıq qaldıqda yapışdırma prosesi zamanı baş verən qüsura aiddir. Buna əskik nöqtə deyilir (1 nöqtədən çox olan köynək astarlı, 2 baldan çox olan digər astar); İsti ərimə yapışdırıcısı tamamilə parça səthinə köçürülmür, nəticədə toz nöqtələri yoxdur və toz sızır.
Həddindən artıq örtük
Həddindən artıq örtük, həmçinin çox örtük kimi tanınan, yapışan astarın lokallaşdırılmış sahəsidir. Tətbiq edilən isti əriyən yapışqanın faktiki miqdarı qeyd olunan məbləğdən əhəmiyyətli dərəcədə çoxdur və tətbiq olunan isti əriyən yapışdırıcının vahid sahəsinin tətbiq olunan isti əriyən yapışdırıcının göstərilən vahid sahəsindən 12% böyük olması kimi özünü göstərir.
Qeyri-bərabər örtük
Qapağın qeyri-bərabərliyi kimi də tanınan örtük qeyri-bərabərliyi, yapışan astarın sol, orta, sağ və ya ön və arxa hissəsinə tətbiq olunan yapışdırıcının miqdarının əhəmiyyətli dərəcədə fərqli olduğu bir qüsur təzahürüdür.
Pudralama
Qapaq bağlaması, həmçinin örtük bağlaması kimi tanınan, isti əriyən yapışdırıcının normal örtük nöqtəsindən əhəmiyyətli dərəcədə böyük olan parçaya köçürülməsi zamanı örtük prosesi zamanı əmələ gələn bir yapışan nöqtə və ya blok növüdür.
Toz tökülməsi
Dökülmə tozu, həmçinin tökmə tozu olaraq bilinir, substrat ilə yapışmayan yapışan astarlı parça strukturunda qalan yapışan tozdur. Və ya əsas parça və ətrafdakı yapışan toz ilə birləşməmiş, tətbiq olunan isti əriyən yapışqanın tam bişməməsi nəticəsində əmələ gələn yapışqan tozu.
Bundan əlavə, paça qüsurları, yer qüsurları, diaqonal qüsurlar, quş gözü naxış qüsurları, tağlar, qırıq başlar, naxış rəng səhvləri, qırıq toxunma qüsurları, aşınma qüsurları, ləkə qüsurları, asma kənar qüsurları və s. Bu qüsurlar iplik keyfiyyəti, toxuculuq prosesi, boyama müalicəsi və s. kimi müxtəlif amillərlə bağlı ola bilər.
Göndərmə vaxtı: 24 iyun 2024-cü il