Die Inspektion galvanisierter Anschlussprodukte ist eine unverzichtbare Aufgabe nach Abschluss der Galvanisierung. Nur die galvanisierten Produkte, die die Prüfung bestehen, können zur Verwendung an den nächsten Prozess übergeben werden.
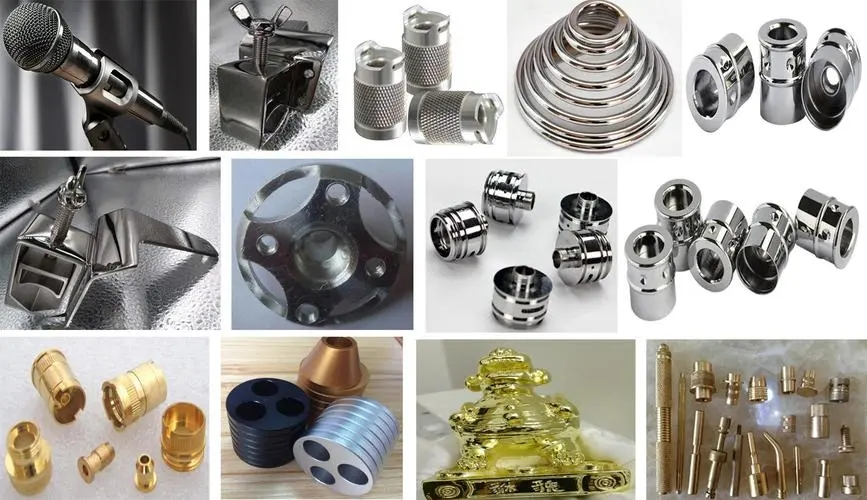
Normalerweise sind die Prüfpunkte für galvanisierte Produkte: Filmdicke, Haftung, Lötfähigkeit, Aussehen, Verpackung und Salzsprühtest. Für Produkte mit besonderen Anforderungen an Zeichnungen gibt es Porositätstests (30U“) für Gold mit der Salpetersäuredampfmethode, palladiumbeschichtete Nickelprodukte (mit der Gelelektrolysemethode) oder andere Umwelttests.
1. Inspektion des Galvanisierungsprodukts – Inspektion der Filmdicke
1. Die Filmdicke ist ein grundlegendes Element für die Galvanikprüfung. Das verwendete Grundgerät ist ein Fluoreszenzfilmdickenmessgerät (Röntgen). Das Prinzip besteht darin, die Beschichtung mit Röntgenstrahlen zu bestrahlen, das von der Beschichtung zurückgegebene Energiespektrum zu erfassen und die Dicke und Zusammensetzung der Beschichtung zu ermitteln.
2. Vorsichtsmaßnahmen bei der Verwendung von Röntgenstrahlen:
1) Die Spektrumkalibrierung ist jedes Mal erforderlich, wenn Sie den Computer einschalten
2) Führen Sie jeden Monat eine Fadenkreuzkalibrierung durch
3) Die Gold-Nickel-Kalibrierung sollte mindestens einmal pro Woche durchgeführt werden
4) Bei der Messung sollte die Testdatei entsprechend dem im Produkt verwendeten Stahl ausgewählt werden.
5) Für neue Produkte, für die keine Testdatei vorhanden ist, sollte eine Testdatei erstellt werden.
3. Die Bedeutung von Testdateien:
Beispiel: Au-Ni-Cu(100-221 sn 4%@0,2 cfp
Au-Ni-Cu – Testen Sie die Dicke der Nickelbeschichtung und anschließend der Goldbeschichtung auf dem Kupfersubstrat.
(100-221 sn 4 % – AMP-Kupfermaterialnummer Kupfer mit 4 % Zinn)

2. Inspektion des Galvanisierungsprodukts und Haftungsprüfung
Die Haftungsprüfung ist ein notwendiger Prüfpunkt für galvanische Produkte. Schlechte Haftung ist der häufigste Fehler bei der Inspektion galvanischer Produkte. Normalerweise gibt es zwei Inspektionsmethoden:
1. Biegemethode: Verwenden Sie zunächst ein Kupferblech mit der gleichen Dicke wie der erforderliche Erkennungsanschluss, um den zu biegenden Bereich zu polstern, biegen Sie die Probe mit einer Flachzange um 180 Grad und beobachten Sie mit einem Mikroskop, ob dies der Fall ist Abblättern oder Abblättern der Beschichtung auf der gebogenen Oberfläche.
2. Klebebandmethode: Kleben Sie das Klebeband mit 3M-Klebeband vertikal im 90-Grad-Winkel fest auf die Oberfläche der zu prüfenden Probe, reißen Sie das Klebeband schnell ab und beobachten Sie, wie sich der Metallfilm vom Klebeband ablöst. Wenn Sie mit Ihren Augen nicht klar sehen können, können Sie zur Beobachtung ein 10-fach-Mikroskop verwenden.
3. Ergebnisermittlung:
a) Es darf kein Metallpulver herunterfallen oder Flickenband anhaften.
b) Die Metallbeschichtung darf sich nicht ablösen.
c) Solange das Grundmaterial nicht gebrochen ist, sollte es nach dem Biegen keine ernsthaften Risse oder Ablösungen geben.
d) Es darf keine Blasenbildung auftreten.
e) Das darunter liegende Metall darf nicht freigelegt werden, ohne dass das Grundmaterial zerbricht.
4. Wenn die Haftung schlecht ist, sollten Sie lernen, die Stelle der abgelösten Schicht zu erkennen. Mit einem Mikroskop und Röntgenstrahlen können Sie die Dicke der abgelösten Beschichtung testen und so den Arbeitsplatz ermitteln, an dem das Problem auftritt.
3. Inspektion des Galvanisierungsprodukts und Prüfung der Lötbarkeit
1.Lötbarkeit ist die grundlegende Funktion und der Zweck von Zinn-Blei und Verzinnung. Wenn Anforderungen an den Nachlötprozess bestehen, ist eine schlechte Schweißung ein schwerwiegender Mangel.
2.Grundlegende Methoden der Lotprüfung:
1) Direktes Eintauchen der Zinnmethode: Tauchen Sie das Lotteil gemäß den Zeichnungen direkt in das erforderliche Flussmittel und tauchen Sie es in einen 235-Grad-Zinnofen. Nach 5 Sekunden sollte es langsam mit einer Geschwindigkeit von etwa 25 mm/s herausgenommen werden. Kühlen Sie es nach dem Herausnehmen auf normale Temperatur ab und beobachten und beurteilen Sie es mit einem 10-fach-Mikroskop: Der verzinnte Bereich sollte größer als 95 % sein, der verzinnte Bereich sollte glatt und sauber sein und es dürfen keine Lötrückstände, Entlötungen, Nadellöcher usw. vorhanden sein andere Phänomene, was bedeutet, dass es qualifiziert ist.
2) Zuerst altern und dann schweißen. Bei Produkten mit besonderen Anforderungen an bestimmte Kraftoberflächen sollten die Proben vor dem Schweißtest 8 oder 16 Stunden lang mit einer Dampfalterungsmaschine gealtert werden, um die Leistung des Produkts in rauen Einsatzumgebungen zu bestimmen. Schweißleistung.
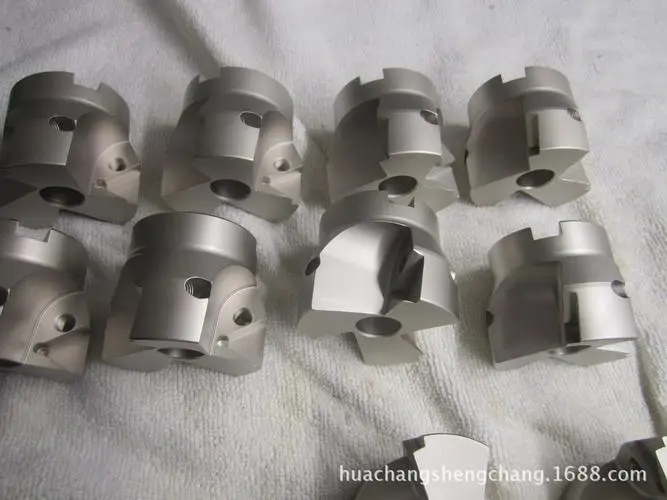
4. Inspektion des galvanischen Produkts – Inspektion des Aussehens
1. Die Prüfung des Aussehens ist der grundlegende Prüfpunkt der Galvanikprüfung. Anhand des Erscheinungsbilds können wir die Eignung der Galvanisierungsprozessbedingungen und mögliche Änderungen in der Galvanisierungslösung erkennen. Unterschiedliche Kunden haben unterschiedliche Anforderungen an das Erscheinungsbild. Alle galvanisierten Anschlüsse sollten mit einem mindestens zehnfach größeren Mikroskop untersucht werden. Bei aufgetretenen Mängeln ist es umso hilfreicher, die Ursache des Problems zu analysieren, je größer die Vergrößerung ist.
2. Inspektionsschritte:
1). Nehmen Sie die Probe, legen Sie sie unter ein 10-fach-Mikroskop und beleuchten Sie sie vertikal mit einer Standard-Weißlichtquelle:
2). Beobachten Sie den Oberflächenzustand des Produkts durch das Okular.
3. Beurteilungsmethode:
1). Die Farbe sollte einheitlich sein, ohne dunkle oder helle Farbe oder mit unterschiedlichen Farben (wie Schwärzung, Rötung oder Gelbfärbung). Bei der Vergoldung sollte es keinen gravierenden Farbunterschied geben.
2). Lassen Sie keine Fremdkörper (Haarflocken, Staub, Öl, Kristalle) daran haften
3). Es muss trocken sein und darf keine Feuchtigkeitsflecken aufweisen.
4). Gute Glätte, keine Löcher oder Partikel.
5). Es dürfen keine Druckstellen, Kratzer, Kratzer und andere Verformungserscheinungen sowie Beschädigungen an den plattierten Teilen auftreten.
6). Die untere Schicht darf nicht freigelegt werden. Was das Aussehen von Zinn-Blei angeht, sind einige (nicht mehr als 5 %) Grübchen und Grübchen zulässig, solange die Lötbarkeit dadurch nicht beeinträchtigt wird.
7). Die Beschichtung darf keine Blasenbildung, Abblättern oder andere schlechte Haftung aufweisen.
8). Die Galvanikposition ist gemäß den Zeichnungen auszuführen. Der QE-Ingenieur kann beschließen, den Standard angemessen zu lockern, ohne die Funktion zu beeinträchtigen.
9). Bei verdächtigen Erscheinungsfehlern sollte der QE-Ingenieur die Grenzwerte für Muster und Aussehenshilfsmittel festlegen.
5. Inspektion von Galvanikprodukten und Verpackung
Die Prüfung der Verpackung von Galvanikprodukten erfordert, dass die Verpackungsrichtung korrekt ist, die Verpackungsschalen und -kartons sauber und ordentlich sind und keine Beschädigungen vorliegen: Die Etiketten sind vollständig und korrekt und die Anzahl der internen und externen Etiketten ist konsistent.
6.Galvanisierungsproduktinspektion – Salzsprühtest
Nach dem Bestehen des Salzsprühtests wird die Oberfläche nicht qualifizierter galvanisierter Teile schwarz und es bildet sich roter Rost. Natürlich führen unterschiedliche Arten der Galvanisierung zu unterschiedlichen Ergebnissen.
Der Salzsprühtest von Galvanisierungsprodukten ist in zwei Kategorien unterteilt: Die eine ist der Expositionstest in der natürlichen Umgebung; Der andere ist der künstlich beschleunigte, simulierte Salznebel-Umgebungstest. Der künstlich simulierte Salzsprühumgebungstest besteht darin, ein Testgerät mit einem bestimmten Volumenraum – einer Salzsprühtestkammer – zu verwenden, um in seinem Volumenraum künstliche Methoden zu verwenden, um eine Salzsprühumgebung zu schaffen, um die Leistung und Qualität der Salzsprühkorrosionsbeständigkeit zu bewerten das Produkt. .
Zu den künstlich simulierten Salzsprühtests gehören:
1) Der Neutralsalzsprühtest (NSS-Test) ist die früheste beschleunigte Korrosionstestmethode mit dem breitesten Anwendungsbereich. Dabei wird eine 5 %ige Natriumchlorid-Salzlösung verwendet und der pH-Wert der Lösung als Sprühlösung auf einen neutralen Bereich (6 bis 7) eingestellt. Die Testtemperatur beträgt jeweils 35 °C und die Sedimentationsrate des Salznebels muss zwischen 1 und 2 ml/80 cm³/h liegen.
2) Der Acetat-Salzsprühtest (ASS-Test) wurde auf Basis des neutralen Salzsprühtests entwickelt. Dabei wird einer 5 %igen Natriumchloridlösung etwas Eisessig zugesetzt, um den pH-Wert der Lösung auf etwa 3 zu senken, wodurch die Lösung sauer wird und der entstehende Salznebel ebenfalls von neutralem Salznebel zu sauer wechselt. Seine Korrosionsrate ist etwa dreimal schneller als beim NSS-Test.
3) Der Kupfersalz-beschleunigte Acetat-Salzsprühtest (CASS-Test) ist ein kürzlich im Ausland entwickelter schneller Salzsprühkorrosionstest. Die Prüftemperatur beträgt 50°C. Der Salzlösung wird eine kleine Menge Kupfersalz-Kupferchlorid zugesetzt, um eine starke Korrosion hervorzurufen. Seine Korrosionsrate ist etwa achtmal so hoch wie die des NSS-Tests.
Oben sind die Inspektionsstandards und Inspektionsmethoden für galvanisierte Produkte aufgeführt, einschließlich der Inspektion der Filmdicke galvanisierter Produkte, der Haftungsprüfung, der Schweißbarkeitsprüfung, der Prüfung des Aussehens, der Verpackungsprüfung und des Salzsprühtests.
Zeitpunkt der Veröffentlichung: 05.06.2024