A galvanizált végtermékek ellenőrzése a galvanizálás befejezése után elengedhetetlen feladat. Csak az ellenőrzésen átesett galvanizált termékek adhatók át a következő folyamatnak felhasználásra.
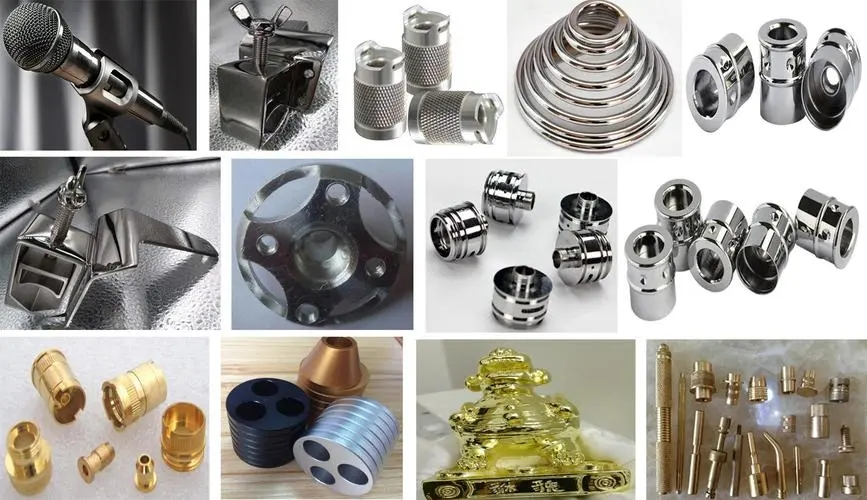
Általában a galvanizált termékek vizsgálati elemei a következők: filmvastagság, tapadás, forrasztási képesség, megjelenés, csomagolás és sópermet teszt. A rajzokon speciális követelményeket támasztó termékeknél porozitási vizsgálatok (30U”) vannak az aranyra salétromsavgőz módszerrel, palládiumozott nikkel termékek (gél elektrolízis módszerrel) vagy egyéb környezeti vizsgálatok.
1. Galvanizálási termék ellenőrzése-filmvastagság ellenőrzése
1. A fólia vastagsága a galvanizáló vizsgálat alapvető eleme. Az alapvető használt eszköz egy fluoreszcens filmvastagság mérő (X-RAY). Az alapelv az, hogy röntgensugarak segítségével besugározzák a bevonatot, összegyűjtik a bevonat által visszaadott energiaspektrumot, és azonosítják a bevonat vastagságát és összetételét.
2. Óvintézkedések a röntgensugár használatakor:
1) A spektrum kalibrálása minden alkalommal szükséges, amikor bekapcsolja a számítógépet
2) Végezzen szálkereszt kalibrálást minden hónapban
3) Az arany-nikkel kalibrálást hetente legalább egyszer el kell végezni
4) A mérés során a tesztfájlt a termékben használt acélnak megfelelően kell kiválasztani.
5) Az új termékekhez, amelyek nem rendelkeznek tesztfájllal, tesztfájlt kell létrehozni.
3. A tesztfájlok jelentősége:
Példa: Au-Ni-Cu(100-221 sn 4%@0.2 cfp
Au-Ni-Cu—– Tesztelje a nikkelezés, majd az aranyozás vastagságát rézfelületen.
(100-221 sn 4%—--AMP réz anyagszám 4% ónt tartalmazó réz)

2. Galvanizálási termékellenőrzés-tapadásvizsgálat
A tapadás-ellenőrzés a galvanizáló termékeknél szükséges vizsgálati elem. A gyenge tapadás a leggyakoribb hiba a galvanizáló termék vizsgálatánál. Általában két vizsgálati módszer létezik:
1. Hajlítási módszer: Először használjon a szükséges érzékelő terminál vastagságú rézlapot a hajlítandó terület kipárnázásához, lapos fogóval hajlítsa meg a mintát 180 fokkal, majd mikroszkóp segítségével figyelje meg, hogy a bevonat leválása vagy leválása a hajlított felületen.
2. Szalagos módszer: Használjon 3M szalagot, hogy erősen ragasszon a vizsgálandó minta felületére, függőlegesen 90 fokban, gyorsan tépje le a szalagot, és figyelje meg a szalagról leválódó fémfilmet. Ha nem tud tisztán megfigyelni a szemével, használhat 10-szeres mikroszkópot a megfigyeléshez.
3. Eredmény meghatározása:
a) Ne essen le fémpor vagy ragadjon le a foltszalag.
b) A fémbevonat nem leválhat.
c) Amíg az alapanyag nem törik el, a hajlítás után ne legyen komoly repedés vagy hámlás.
d) Ne legyen bugyborékolás.
e) Nem szabad az alatta lévő fémet kitenni anélkül, hogy az alapanyag eltörne.
4. Ha gyenge a tapadás, meg kell tanulnia megkülönböztetni a lehámlott réteg helyét. Mikroszkóp és röntgen segítségével tesztelheti a hámozott bevonat vastagságát, hogy meghatározza a problémát okozó munkaállomást.
3. Galvanizálási termékellenőrzés-forraszthatósági vizsgálat
1. A forraszthatóság az ón-ólom és az ónozás alapvető funkciója és célja. Ha az utóforrasztási folyamat követelményei vannak, akkor a rossz hegesztés komoly hiba.
2. A forrasztásvizsgálat alapvető módszerei:
1) Közvetlen merítésű ón módszer: A rajzok szerint a forrasztórészt közvetlenül merítse a szükséges folyósítóba és merítse egy 235 fokos bádogkemencébe. 5 másodperc elteltével lassan ki kell venni, körülbelül 25 mm/s sebességgel. Kivétel után hűtsük le normál hőmérsékletre, és 10-szeres mikroszkóp segítségével figyeljük meg és ítéljük meg: az ónozott terület legyen 95%-nál nagyobb, az ónozott terület legyen sima és tiszta, és ne legyen forrasztási selejt, kiforrasztás, tűlyukak és egyéb jelenségek, ami azt jelenti, hogy minősített.
2) Először az öregítés, majd a hegesztés. Azoknál a termékeknél, amelyek bizonyos erőfelületeken speciális követelményeket támasztanak, a mintákat 8 vagy 16 órán át érleltetni kell gőzöregítés-vizsgáló géppel a hegesztési teszt előtt, hogy meghatározzák a termék teljesítményét zord használati körülmények között. Hegesztési teljesítmény.
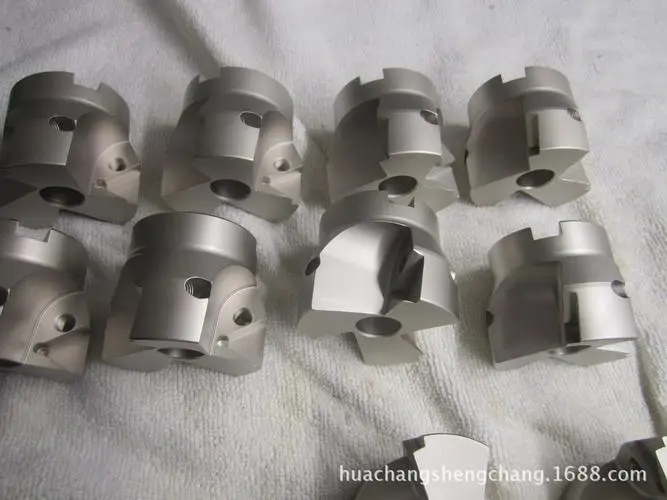
4. Galvanizálási termék ellenőrzése-megjelenési ellenőrzése
1. A megjelenés ellenőrzése a galvanizáló vizsgálat alapvető vizsgálati eleme. A megjelenésből láthatjuk a galvanizáló eljárás körülményeinek megfelelőségét és a galvanizálási megoldás esetleges változásait. A különböző vásárlók eltérő követelményeket támasztanak a megjelenéssel szemben. Minden galvanizált érintkezőt legalább 10-szer nagyobb mikroszkóppal kell megfigyelni. A fellépő hibák esetén minél nagyobb a nagyítás, annál hasznosabb a probléma okának elemzése.
2. Az ellenőrzés lépései:
1). Vegye ki a mintát, helyezze 10-szeres mikroszkóp alá, és függőlegesen világítsa meg szabványos fehér fényforrással:
2). Figyelje meg a termék felületi állapotát a szemlencsén keresztül.
3. Ítéletmód:
1). A színnek egységesnek kell lennie, sötét vagy világos színek nélkül, vagy különböző színekkel (pl. feketedés, vörösség vagy sárgás). Az aranyozásnál nem lehet komoly színkülönbség.
2). Ne hagyja, hogy idegen anyag (hajpehely, por, olaj, kristályok) rátapadjon
3). Száraznak kell lennie, és nem lehet nedvességtől foltos.
4). Jó simaság, nincsenek lyukak vagy részecskék.
5). Nem lehetnek nyomások, karcolások, karcolások és egyéb deformációs jelenségek, valamint a lemezelt részek sérülése.
6). Az alsó réteget nem szabad kitenni. Ami az ón-ólom megjelenését illeti, néhány (legfeljebb 5%) gödör és gödör megengedett mindaddig, amíg az nem befolyásolja a forraszthatóságot.
7). A bevonatnak nem lehet hólyagosodása, hámlása vagy egyéb rossz tapadása.
8). A galvanizáló pozíciót a rajzoknak megfelelően kell elvégezni. A QE mérnök dönthet úgy, hogy megfelelően enyhíti a szabványt, anélkül, hogy a funkciót befolyásolná.
9). Gyanús megjelenési hibák esetén a QE mérnöknek meg kell határoznia a határmintát és a külső megjelenési segédszabványokat.
5. Galvanizálási termékellenőrzés-csomagolásellenőrzés
A galvanizáló termék csomagolásának ellenőrzése megköveteli, hogy a csomagolás iránya megfelelő legyen, a csomagolótálcák és dobozok tiszták, rendezettek, sérülésmentesek: a címkék kitöltöttek és helyesek, a belső és külső címkék száma egységes.
6. Galvanizálási termékellenőrzés-sópermet teszt
A sópermetezési teszten való megfelelés után a nem minősített galvanizált alkatrészek felülete feketévé válik, és vörös rozsda képződik. Természetesen a különböző típusú galvanizálás eltérő eredményeket hoz.
A galvanizáló termékek sóspray-tesztje két kategóriába sorolható: az egyik a természetes környezet expozíciós tesztje; a másik a mesterséges gyorsított szimulált sópermet környezeti teszt. A mesterségesen szimulált sópermet környezeti teszt egy bizonyos térfogatú vizsgálóberendezés - sópermet tesztkamra - használata, annak térfogatterében mesterséges módszerek alkalmazása sópermet környezet létrehozására a sópermet korrózióállósági teljesítményének és minőségének felmérésére. a terméket. .
A mesterséges szimulált sópermet tesztek a következők:
1) A semleges sópermet teszt (NSS-teszt) a legkorábbi gyorsított korróziós vizsgálati módszer a legszélesebb alkalmazási területtel. 5%-os nátrium-klorid sóoldatot használ, az oldat pH-értékét permetező oldatként semleges tartományba (6-7) állítják be. A vizsgálati hőmérséklet 35 ℃, és a sópermet ülepedési sebességének 1-2 ml/80 cm?.h között kell lennie.
2) Az acetát sópermet teszt (ASS teszt) a semleges sópermet teszt alapján kerül kifejlesztésre. Az 5%-os nátrium-klorid oldathoz némi jégecetet ad, hogy az oldat pH-értékét körülbelül 3-ra csökkentse, így az oldat savassá válik, és a keletkező sópermet is semleges sópermetről savasra változik. Korróziós sebessége körülbelül 3-szor gyorsabb, mint az NSS teszté.
3) A réz-só gyorsított acetát-sópermet teszt (CASS-teszt) egy gyors sópermetes korróziós teszt, amelyet nemrégiben fejlesztettek ki külföldön. A vizsgálati hőmérséklet 50°C. A sóoldathoz kis mennyiségű rézsót-réz-kloridot adnak, hogy erősen korróziót idézzenek elő. Korróziós sebessége körülbelül 8-szorosa az NSS-tesztének.
A fentiek a galvanizált termékek ellenőrzési szabványai és vizsgálati módszerei, beleértve a galvanizált termék filmréteg vastagságának ellenőrzését, a tapadás ellenőrzését, a hegeszthetőség ellenőrzését, a megjelenés ellenőrzését, a csomagolás ellenőrzését, a sópermet tesztet,
Feladás időpontja: 2024-05-05