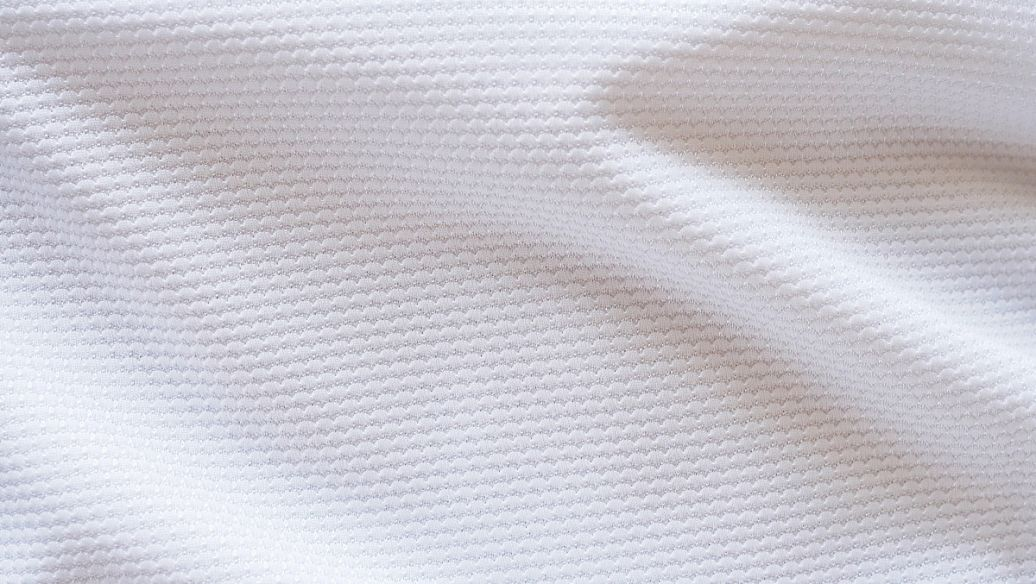
ಲೈನಿಂಗ್ ಫ್ಯಾಬ್ರಿಕ್ ತಯಾರಿಕೆಯ ಪ್ರಕ್ರಿಯೆಯಲ್ಲಿ, ದೋಷಗಳ ನೋಟವು ಅನಿವಾರ್ಯವಾಗಿದೆ. ದೋಷಗಳನ್ನು ತ್ವರಿತವಾಗಿ ಗುರುತಿಸುವುದು ಮತ್ತು ದೋಷಗಳ ಪ್ರಕಾರಗಳು ಮತ್ತು ಗಾತ್ರಗಳನ್ನು ಪ್ರತ್ಯೇಕಿಸುವುದು ಹೇಗೆ ಎಂಬುದು ಬಟ್ಟೆಯ ಒಳಪದರದ ಗುಣಮಟ್ಟವನ್ನು ಮೌಲ್ಯಮಾಪನ ಮಾಡಲು ನಿರ್ಣಾಯಕವಾಗಿದೆ.
ಬಟ್ಟೆ ಲೈನಿಂಗ್ ಫ್ಯಾಬ್ರಿಕ್ನಲ್ಲಿ ಸಾಮಾನ್ಯ ದೋಷಗಳು
ರೇಖೀಯ ದೋಷಗಳು
ರೇಖೆಯ ದೋಷಗಳು, ರೇಖೆಯ ದೋಷಗಳು ಎಂದೂ ಕರೆಯಲ್ಪಡುತ್ತವೆ, ಅವುಗಳು ರೇಖಾಂಶ ಅಥವಾ ಅಡ್ಡ ದಿಕ್ಕುಗಳಲ್ಲಿ ವಿಸ್ತರಿಸುವ ಮತ್ತು 0.3cm ಗಿಂತ ಹೆಚ್ಚಿನ ಅಗಲವನ್ನು ಹೊಂದಿರುವ ದೋಷಗಳಾಗಿವೆ. ಇದು ಸಾಮಾನ್ಯವಾಗಿ ನೂಲಿನ ಗುಣಮಟ್ಟ ಮತ್ತು ನೇಯ್ಗೆ ತಂತ್ರಜ್ಞಾನಕ್ಕೆ ಸಂಬಂಧಿಸಿದೆ, ಉದಾಹರಣೆಗೆ ಅಸಮ ನೂಲು ದಪ್ಪ, ಕಳಪೆ ಟ್ವಿಸ್ಟ್, ಅಸಮ ನೇಯ್ಗೆ ಒತ್ತಡ ಮತ್ತು ಅಸಮರ್ಪಕ ಸಲಕರಣೆ ಹೊಂದಾಣಿಕೆ.
ಸ್ಟ್ರಿಪ್ ದೋಷಗಳು
ಸ್ಟ್ರಿಪ್ ದೋಷಗಳು, ಸ್ಟ್ರಿಪ್ ದೋಷಗಳು ಎಂದೂ ಕರೆಯಲ್ಪಡುತ್ತವೆ, ಅವುಗಳು ರೇಖಾಂಶ ಅಥವಾ ಅಡ್ಡ ದಿಕ್ಕುಗಳ ಉದ್ದಕ್ಕೂ ವಿಸ್ತರಿಸುವ ದೋಷಗಳಾಗಿವೆ ಮತ್ತು 0.3cm ಗಿಂತ ಹೆಚ್ಚಿನ ಅಗಲವನ್ನು ಹೊಂದಿರುತ್ತವೆ (ಬ್ಲಾಕಿ ದೋಷಗಳನ್ನು ಒಳಗೊಂಡಂತೆ). ಇದು ಸಾಮಾನ್ಯವಾಗಿ ನೂಲು ಗುಣಮಟ್ಟ ಮತ್ತು ಮಗ್ಗದ ನಿಯತಾಂಕಗಳ ಅಸಮರ್ಪಕ ಸೆಟ್ಟಿಂಗ್ಗಳಂತಹ ಅಂಶಗಳಿಗೆ ಸಂಬಂಧಿಸಿದೆ.
ಹಾನಿಯಾಗುತ್ತದೆ
ಡ್ಯಾಮೇಜಿಂಗ್ ಎನ್ನುವುದು ವಾರ್ಪ್ ಮತ್ತು ನೇಯ್ಗೆ (ರೇಖಾಂಶ ಮತ್ತು ಅಡ್ಡ) ದಿಕ್ಕುಗಳಲ್ಲಿ ಎರಡು ಅಥವಾ ಹೆಚ್ಚಿನ ನೂಲುಗಳು ಅಥವಾ 0.2cm2 ಅಥವಾ ಹೆಚ್ಚಿನ ರಂಧ್ರಗಳನ್ನು ಒಡೆಯುವುದನ್ನು ಸೂಚಿಸುತ್ತದೆ, ಅಂಚಿನಿಂದ 2cm ಅಥವಾ ಅದಕ್ಕಿಂತ ಹೆಚ್ಚಿನ ಮುರಿದ ಅಂಚುಗಳು ಮತ್ತು 0.3cm ಅಥವಾ ಹೆಚ್ಚಿನ ಹೂವುಗಳನ್ನು ಜಿಗಿಯುವುದು. ಹಾನಿಯ ಕಾರಣಗಳು ವೈವಿಧ್ಯಮಯವಾಗಿವೆ, ಸಾಮಾನ್ಯವಾಗಿ ಸಾಕಷ್ಟು ನೂಲಿನ ಶಕ್ತಿ, ವಾರ್ಪ್ ಅಥವಾ ನೇಯ್ಗೆ ನೂಲುಗಳಲ್ಲಿನ ಅತಿಯಾದ ಒತ್ತಡ, ನೂಲು ಉಡುಗೆ, ಯಂತ್ರದ ಅಸಮರ್ಪಕ ಕಾರ್ಯಗಳು ಮತ್ತು ಅಸಮರ್ಪಕ ಕಾರ್ಯಾಚರಣೆಗೆ ಸಂಬಂಧಿಸಿವೆ.
ಬೇಸ್ ಫ್ಯಾಬ್ರಿಕ್ನಲ್ಲಿ ದೋಷಗಳು
ಬೇಸ್ ಫ್ಯಾಬ್ರಿಕ್ನಲ್ಲಿನ ದೋಷಗಳು, ಬೇಸ್ ಫ್ಯಾಬ್ರಿಕ್ನಲ್ಲಿನ ದೋಷಗಳು ಎಂದೂ ಕರೆಯಲ್ಪಡುತ್ತವೆ, ಇದು ಬಟ್ಟೆ ಲೈನಿಂಗ್ ಫ್ಯಾಬ್ರಿಕ್ನ ಉತ್ಪಾದನಾ ಪ್ರಕ್ರಿಯೆಯಲ್ಲಿ ಸಂಭವಿಸುವ ದೋಷಗಳಾಗಿವೆ.
ಫಿಲ್ಮ್ ಫೋಮಿಂಗ್
ಫಿಲ್ಮ್ ಬ್ಲಿಸ್ಟರಿಂಗ್, ಫಿಲ್ಮ್ ಬ್ಲಿಸ್ಟರಿಂಗ್ ಎಂದೂ ಕರೆಯಲ್ಪಡುವ ದೋಷವಾಗಿದ್ದು, ಫಿಲ್ಮ್ ತಲಾಧಾರಕ್ಕೆ ದೃಢವಾಗಿ ಅಂಟಿಕೊಳ್ಳುವುದಿಲ್ಲ, ಇದು ಗುಳ್ಳೆಗಳಿಗೆ ಕಾರಣವಾಗುತ್ತದೆ.
ಸುಡುವಿಕೆ
ಒಣಗಿಸುವ ಸೀಲಿಂಗ್ ಎನ್ನುವುದು ಲೈನಿಂಗ್ ಫ್ಯಾಬ್ರಿಕ್ನ ಮೇಲ್ಮೈಯಲ್ಲಿ ದೋಷವಾಗಿದ್ದು ಅದು ಹಳದಿ ಬಣ್ಣದಲ್ಲಿ ಸುಟ್ಟುಹೋಗುತ್ತದೆ ಮತ್ತು ದೀರ್ಘಾವಧಿಯ ಹೆಚ್ಚಿನ ತಾಪಮಾನದ ಕಾರಣದಿಂದಾಗಿ ಗಟ್ಟಿಯಾದ ವಿನ್ಯಾಸವನ್ನು ಹೊಂದಿರುತ್ತದೆ.
ಗಟ್ಟಿಗೊಳಿಸು
ಗಟ್ಟಿಯಾಗುವುದು, ಗಟ್ಟಿಯಾಗುವುದು ಎಂದೂ ಕರೆಯಲ್ಪಡುತ್ತದೆ, ಲೈನಿಂಗ್ ಫ್ಯಾಬ್ರಿಕ್ ಅದರ ಮೂಲ ಸ್ಥಿತಿಗೆ ಮರಳಲು ಮತ್ತು ಸಂಕುಚಿತಗೊಂಡ ನಂತರ ಅದರ ವಿನ್ಯಾಸವನ್ನು ಗಟ್ಟಿಯಾಗಿಸಲು ಅಸಮರ್ಥತೆಯನ್ನು ಸೂಚಿಸುತ್ತದೆ.
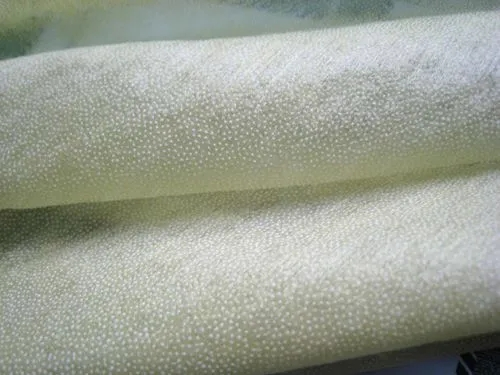
ಪೌಡರ್ ಸೋರಿಕೆ ಮತ್ತು ಸೋರಿಕೆ ಬಿಂದುಗಳು
ಪೌಡರ್ ಸೋರಿಕೆ ಎಂದೂ ಕರೆಯಲ್ಪಡುವ ಲೇಪನ ಕಾಣೆಯಾಗಿದೆ, ಬಿಸಿ ಕರಗುವ ಅಂಟಿಕೊಳ್ಳುವ ಬಿಂದು ಪ್ರಕಾರವು ಅಂಟಿಕೊಳ್ಳುವ ಲೈನಿಂಗ್ನ ಸ್ಥಳೀಯ ಪ್ರದೇಶದಲ್ಲಿ ಬಟ್ಟೆಯ ಕೆಳಭಾಗಕ್ಕೆ ವರ್ಗಾಯಿಸದಿದ್ದಾಗ ಅಂಟಿಸುವ ಪ್ರಕ್ರಿಯೆಯಲ್ಲಿ ಸಂಭವಿಸುವ ದೋಷವನ್ನು ಸೂಚಿಸುತ್ತದೆ ಮತ್ತು ಕೆಳಭಾಗವು ಬಹಿರಂಗಗೊಳ್ಳುತ್ತದೆ. ಇದನ್ನು ಮಿಸ್ಸಿಂಗ್ ಪಾಯಿಂಟ್ ಎಂದು ಕರೆಯಲಾಗುತ್ತದೆ (1 ಪಾಯಿಂಟ್ಗಿಂತ ಹೆಚ್ಚಿನ ಶರ್ಟ್ ಲೈನಿಂಗ್, 2 ಕ್ಕಿಂತ ಹೆಚ್ಚು ಪಾಯಿಂಟ್ಗಳೊಂದಿಗೆ ಇತರ ಲೈನಿಂಗ್); ಬಿಸಿ ಕರಗುವ ಅಂಟಿಕೊಳ್ಳುವಿಕೆಯು ಸಂಪೂರ್ಣವಾಗಿ ಬಟ್ಟೆಯ ಮೇಲ್ಮೈಗೆ ವರ್ಗಾವಣೆಯಾಗುವುದಿಲ್ಲ, ಇದರ ಪರಿಣಾಮವಾಗಿ ಪುಡಿ ಬಿಂದುಗಳು ಮತ್ತು ಪುಡಿ ಸೋರಿಕೆಯು ಕಾಣೆಯಾಗಿದೆ.
ಅತಿಯಾದ ಲೇಪನ
ಮಿತಿಮೀರಿದ ಲೇಪನವನ್ನು ಓವರ್ ಕೋಟಿಂಗ್ ಎಂದೂ ಕರೆಯುತ್ತಾರೆ, ಇದು ಅಂಟಿಕೊಳ್ಳುವ ಲೈನಿಂಗ್ನ ಸ್ಥಳೀಯ ಪ್ರದೇಶವಾಗಿದೆ. ಅನ್ವಯಿಸಲಾದ ಬಿಸಿ ಕರಗುವ ಅಂಟಿಕೊಳ್ಳುವಿಕೆಯ ನಿಜವಾದ ಪ್ರಮಾಣವು ನಿರ್ದಿಷ್ಟಪಡಿಸಿದ ಪ್ರಮಾಣಕ್ಕಿಂತ ಗಣನೀಯವಾಗಿ ಹೆಚ್ಚಾಗಿರುತ್ತದೆ, ಬಿಸಿ ಕರಗುವ ಅಂಟಿಕೊಳ್ಳುವಿಕೆಯ ಘಟಕದ ಪ್ರದೇಶವು ಅನ್ವಯಿಸಲಾದ ಬಿಸಿ ಕರಗುವ ಅಂಟಿಕೊಳ್ಳುವಿಕೆಯ ನಿರ್ದಿಷ್ಟ ಘಟಕದ ಪ್ರದೇಶಕ್ಕಿಂತ 12% ಹೆಚ್ಚಾಗಿರುತ್ತದೆ ಎಂದು ಪ್ರಕಟವಾಗುತ್ತದೆ.
ಅಸಮ ಲೇಪನ
ಲೇಪನದ ಅಸಮಾನತೆ, ಲೇಪನದ ಅಸಮಾನತೆ ಎಂದೂ ಕರೆಯಲ್ಪಡುತ್ತದೆ, ಇದು ದೋಷದ ಅಭಿವ್ಯಕ್ತಿಯಾಗಿದ್ದು, ಅಂಟಿಕೊಳ್ಳುವ ಒಳಪದರದ ಎಡ, ಮಧ್ಯ, ಬಲ ಅಥವಾ ಮುಂಭಾಗ ಮತ್ತು ಹಿಂಭಾಗಕ್ಕೆ ಅನ್ವಯಿಸಲಾದ ಅಂಟಿಕೊಳ್ಳುವಿಕೆಯ ಪ್ರಮಾಣವು ಗಮನಾರ್ಹವಾಗಿ ಭಿನ್ನವಾಗಿರುತ್ತದೆ.
ಪುಡಿ ಮಾಡುವುದು
ಕೋಟಿಂಗ್ ಬಾಂಡಿಂಗ್, ಇದನ್ನು ಲೇಪನ ಬಂಧ ಎಂದೂ ಕರೆಯುತ್ತಾರೆ, ಇದು ಬಿಸಿ ಕರಗುವ ಅಂಟಿಕೊಳ್ಳುವಿಕೆಯನ್ನು ಫ್ಯಾಬ್ರಿಕ್ಗೆ ವರ್ಗಾಯಿಸಿದಾಗ ಲೇಪನ ಪ್ರಕ್ರಿಯೆಯಲ್ಲಿ ರೂಪುಗೊಂಡ ಒಂದು ರೀತಿಯ ಅಂಟಿಕೊಳ್ಳುವ ಬಿಂದು ಅಥವಾ ಬ್ಲಾಕ್ ಆಗಿದೆ, ಇದು ಸಾಮಾನ್ಯ ಲೇಪನ ಬಿಂದುಕ್ಕಿಂತ ಗಮನಾರ್ಹವಾಗಿ ದೊಡ್ಡದಾಗಿದೆ.
ಪುಡಿ ಚೆಲ್ಲುವುದು
ಶೆಡ್ ಪೌಡರ್, ಶೆಡ್ ಪೌಡರ್ ಎಂದೂ ಕರೆಯುತ್ತಾರೆ, ಇದು ತಲಾಧಾರದೊಂದಿಗೆ ಬಂಧಿಸದ ಅಂಟಿಕೊಳ್ಳುವ ಲೈನಿಂಗ್ ಫ್ಯಾಬ್ರಿಕ್ ರಚನೆಯಲ್ಲಿ ಉಳಿದಿರುವ ಅಂಟಿಕೊಳ್ಳುವ ಪುಡಿಯಾಗಿದೆ. ಅಥವಾ ಬೇಸ್ ಫ್ಯಾಬ್ರಿಕ್ ಮತ್ತು ಸುತ್ತಮುತ್ತಲಿನ ಅಂಟಿಕೊಳ್ಳುವ ಪುಡಿಯೊಂದಿಗೆ ಸಂಯೋಜಿಸದ ಅನ್ವಯಿಕ ಬಿಸಿ ಕರಗುವ ಅಂಟಿಕೊಳ್ಳುವಿಕೆಯ ಅಪೂರ್ಣ ಬೇಕಿಂಗ್ ಕಾರಣ ಅಂಟಿಕೊಳ್ಳುವ ಪುಡಿ ರೂಪುಗೊಂಡಿತು.
ಇದರ ಜೊತೆಗೆ, ಕ್ರೋಚ್ ದೋಷಗಳು, ನೆಲದ ದೋಷಗಳು, ಕರ್ಣೀಯ ದೋಷಗಳು, ಪಕ್ಷಿ ಕಣ್ಣಿನ ಮಾದರಿ ದೋಷಗಳು, ಕಮಾನುಗಳು, ಮುರಿದ ತಲೆಗಳು, ಮಾದರಿಯ ಬಣ್ಣ ದೋಷಗಳು, ಮುರಿದ ನೇಯ್ಗೆ ದೋಷಗಳು, ಸವೆತ ದೋಷಗಳು, ಚುಕ್ಕೆ ದೋಷಗಳು, ನೇತಾಡುವ ಅಂಚಿನ ದೋಷಗಳು ಇತ್ಯಾದಿಗಳಂತಹ ವಿವಿಧ ಸಮಸ್ಯೆಗಳೂ ಇರಬಹುದು. ಈ ದೋಷಗಳು ನೂಲಿನ ಗುಣಮಟ್ಟ, ನೇಯ್ಗೆ ಪ್ರಕ್ರಿಯೆ, ಡೈಯಿಂಗ್ ಚಿಕಿತ್ಸೆ ಇತ್ಯಾದಿಗಳಂತಹ ವಿವಿಧ ಅಂಶಗಳಿಗೆ ಸಂಬಂಧಿಸಿರಬಹುದು.
ಪೋಸ್ಟ್ ಸಮಯ: ಜೂನ್-24-2024