In recent years, the industrialization of drones has been sparking and unstoppable. Research firm Goldman Sachs predicts that the drone market will have the opportunity to reach US$100 billion by 2020.
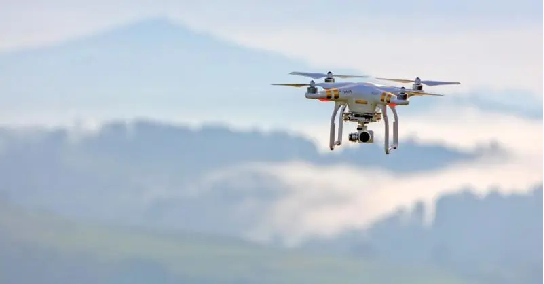
01 Drone inspection standards
At present, there are more than 300 units engaged in the civil drone industry in my country, including about 160 large-scale enterprises, which have formed a complete R&D, manufacturing, sales and service system. In order to regulate the civilian drone industry, the country has gradually improved the corresponding national standard requirements.
UAV electromagnetic compatibility inspection standards
GB/17626-2006 electromagnetic compatibility series standards;
GB/9254-2008 Radio disturbance limits and measurement methods for information technology equipment;
GB/T17618-2015 Information technology equipment immunity limits and measurement methods.
Drone information security inspection standards
GB/T 20271-2016 Information security technology general security technical requirements for information systems;
YD/T 2407-2013 Technical requirements for security capabilities of mobile intelligent terminals;
QJ 20007-2011 General specifications for satellite navigation and navigation receiving equipment.
Drone safety inspection standards
GB 16796-2009 Safety requirements and test methods for security alarm equipment.
02 UAV inspection items and technical requirements
Drone inspection has high technical requirements. The following are the main items and technical requirements for drone inspection:
Flight parameter inspection
The inspection of flight parameters mainly includes maximum flight altitude, maximum endurance time, flight radius, maximum horizontal flight speed, track control accuracy, manual remote control distance, wind resistance, maximum climb speed, etc.
Maximum horizontal flight speed inspection
Under normal operating conditions, the drone rises to an altitude of 10 meters and records the distance S1 displayed on the controller at this time;
The drone flies horizontally at the maximum speed for 10 seconds, and records the distance S2 displayed on the controller at this time;
Calculate the maximum horizontal flight speed according to formula (1).
Formula 1: V=(S2-S1)/10
Note: V is the maximum horizontal flight speed, in meters per second (m/s); S1 is the initial distance displayed on the controller, in meters (m); S2 is the final distance displayed on the controller, in meters (m).
Maximum flight altitude inspection
Under normal operating conditions, the drone rises to an altitude of 10 meters and records the height H1 displayed on the controller at this time;
Then line the height and record the height H2 displayed on the controller at this time;
Calculate the maximum flight altitude according to formula (2).
Formula 2: H=H2-H1
Note: H is the maximum flight height of the drone, in meters (m); H1 is the initial flight height displayed on the controller, in meters (m); H2 is the final flight height displayed on the controller, in meters (m).
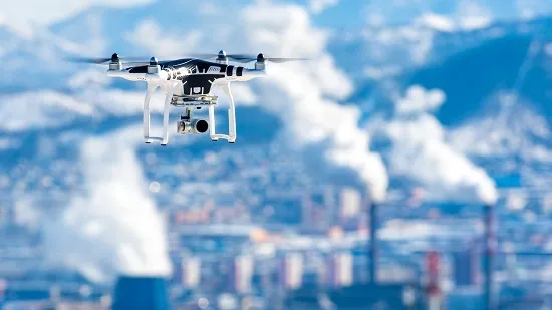
Maximum battery life test
Use a fully charged battery for inspection, raise the drone to a height of 5 meters and hover, use a stopwatch to start timing, and stop timing when the drone automatically descends. The recorded time is the maximum battery life.
Flight radius inspection
The flight distance displayed on the recording controller refers to the flight distance of the drone from launch to return. The flight radius is the flight distance recorded on the controller divided by 2.
flight path inspection
Draw a circle with a diameter of 2m on the ground; lift the drone from the circle point to 10 meters and hover for 15 minutes. Monitor whether the vertical projection position of the drone exceeds this circle during hovering. If the vertical projection position does not exceed this circle, the horizontal track control accuracy is ≤1m; raise the drone to a height of 50 meters and then hover for 10 minutes, and record the maximum and minimum height values displayed on the controller during the hovering process. The value of the two heights minus the height when hovering is the vertical track control accuracy. Vertical track control accuracy should be <10m.
Remote control distance inspection
That is, you can check on the computer or APP that the drone has flown to the distance specified by the operator, and you should be able to control the flight of the drone through the computer/APP.
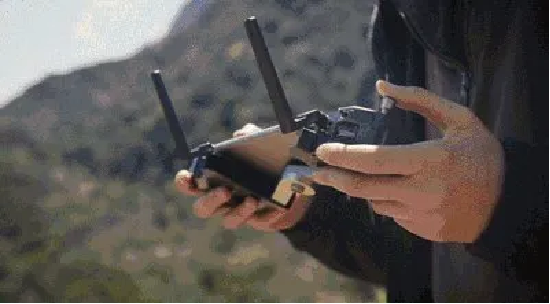
Wind resistance test
Requirements: Normal take-off, landing and flight are possible in winds not less than level 6.
Positioning accuracy inspection
The positioning accuracy of drones depends on the technology, and the range of accuracy that different drones can achieve will vary. Test according to the working status of the sensor and the accuracy range marked on the product.
Vertical: ±0.1m (when visual positioning is working normally); ± 0.5m (when GPS is working normally);
Horizontal: ± 0.3m (when visual positioning is working normally); ± 1.5m (when GPS is working normally);
Insulation resistance test
Refer to the inspection method specified in GB16796-2009 Clause 5.4.4.1. With the power switch turned on, apply a 500 V DC voltage between the power incoming terminal and the exposed metal parts of the housing for 5 seconds and measure the insulation resistance immediately. If the shell has no conductive parts, the device's shell should be covered with a layer of metal conductor, and the insulation resistance between the metal conductor and the power input terminal should be measured. The insulation resistance measurement value should be ≥5MΩ.
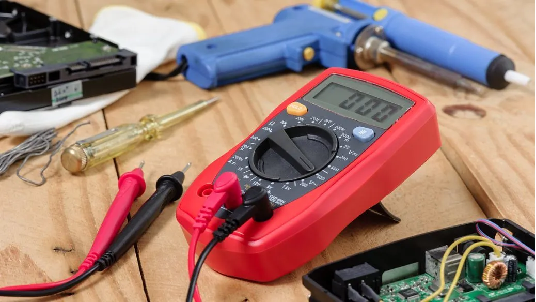
Electrical strength test
Referring to the test method specified in GB16796-2009 clause 5.4.3, the electric strength test between the power inlet and the exposed metal parts of the casing should be able to withstand the AC voltage specified in the standard, which lasts for 1 minute. There should be no breakdown or arcing.
Reliability check
The working time before the first failure is ≥ 2 hours, multiple repeated tests are allowed, and each test time is not less than 15 minutes.
High and low temperature testing
Since the environmental conditions in which drones operate are often changeable and complex, and each aircraft model has different capabilities to control internal power consumption and heat, ultimately resulting in the aircraft's own hardware adapting to temperature differently, so in order to meet For more or operation requirements under specific conditions, flight inspection under high and low temperature conditions is necessary. The high and low temperature inspection of drones requires the use of instruments.
Heat resistance test
Refer to the test method specified in clause 5.6.2.1 of GB16796-2009. Under normal working conditions, use a point thermometer or any suitable method to measure the surface temperature after 4 hours of operation. The temperature rise of accessible parts should not exceed the specified value under normal working conditions in Table 2 of GB8898-2011.
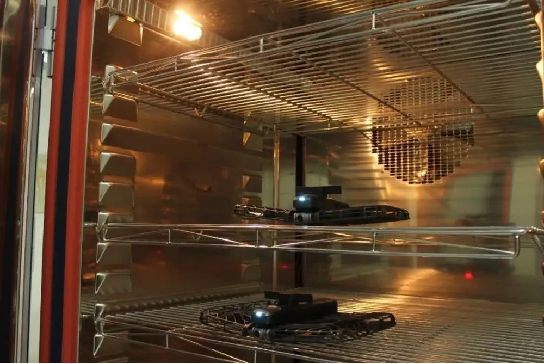
Low temperature inspection
According to the test method specified in GB/T 2423.1-2008, the drone was placed in the environmental test box at a temperature of (-25±2)°C and a test time of 16 hours. After the test is completed and restored under standard atmospheric conditions for 2 hours, the drone should be able to work normally.
Vibration test
According to the inspection method specified in GB/T2423.10-2008:
The drone is in non-working condition and unpackaged;
Frequency range: 10Hz ~ 150Hz;
Crossover frequency: 60Hz;
f<60Hz, constant amplitude 0.075mm;
f>60Hz, constant acceleration 9.8m/s2 (1g);
Single point of control;
The number of scan cycles per axis is l0.
The inspection must be carried out on the bottom of the drone and the inspection time is 15 minutes. After the inspection, the drone should have no obvious appearance damage and be able to operate normally.
Drop test
The drop test is a routine test that most products currently need to do. On the one hand, it is to check whether the packaging of the drone product can protect the product itself well to ensure transportation safety; on the other hand, it is actually the hardware of the aircraft. reliability.
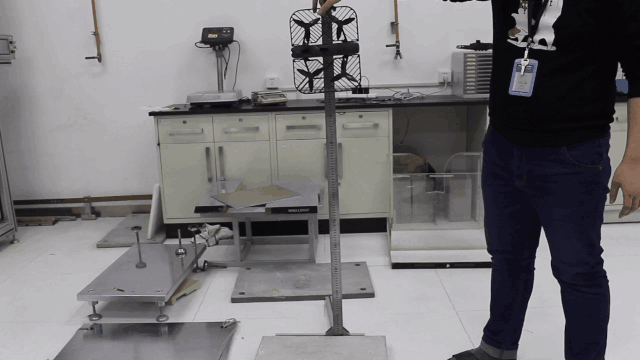
pressure test
Under maximum usage intensity, the drone is subjected to stress tests such as distortion and load-bearing. After the test is completed, the drone needs to be able to continue to work normally.

life span test
Conduct life tests on the drone's gimbal, visual radar, power button, buttons, etc., and the test results must comply with product regulations.
Wear resistance test
Use RCA paper tape for abrasion resistance testing, and the test results should comply with the abrasion requirements marked on the product.
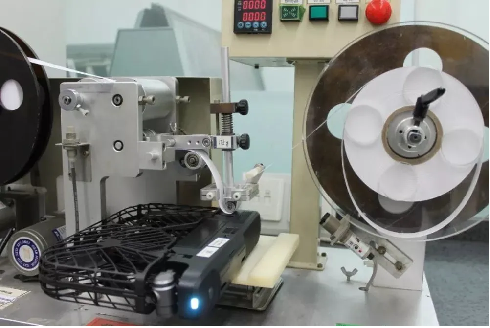
Other routine tests
Such as appearance, packaging inspection, complete assembly inspection, important components and internal inspection, labeling, marking, printing inspection, etc.
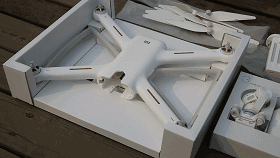
Post time: May-24-2024