Kontrola galwanizowanych wyrobów końcowych jest niezbędnym zadaniem po zakończeniu galwanizacji. Do dalszego procesu mogą zostać przekazane wyłącznie wyroby galwaniczne, które przejdą kontrolę.
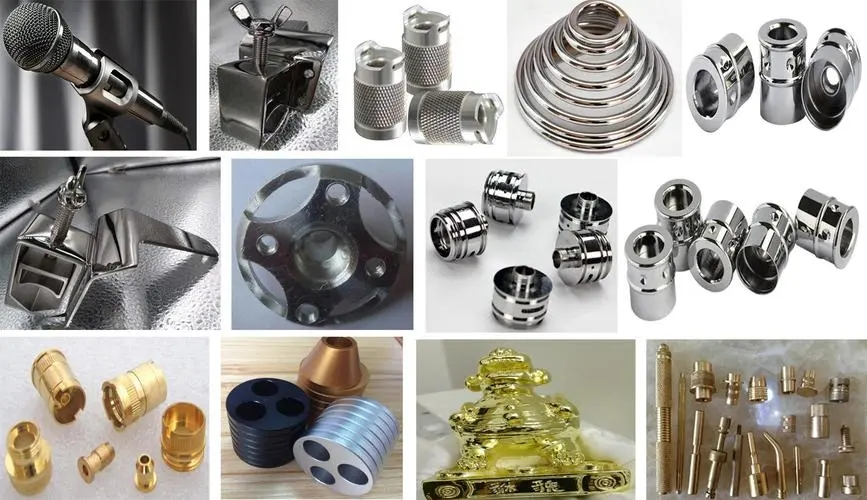
Zwykle elementami kontroli produktów galwanizowanych są: grubość warstwy, przyczepność, zdolność lutowania, wygląd, opakowanie i test mgły solnej. Dla wyrobów o specjalnych wymaganiach na rysunkach przeprowadza się badania porowatości (30U) złota metodą w oparach kwasu azotowego, wyrobów niklowych platerowanych palladem (metodą elektrolizy żelowej) lub inne badania środowiskowe.
1. Kontrola produktu galwanicznego - kontrola grubości folii
1. Grubość folii jest podstawowym elementem kontroli galwanizacji. Podstawowym narzędziem jest miernik grubości warstwy fluorescencyjnej (RTG). Zasadą jest wykorzystanie promieni rentgenowskich do napromieniania powłoki, zebranie widma energii odbitej przez powłokę oraz określenie grubości i składu powłoki.
2. Środki ostrożności podczas korzystania z promieni rentgenowskich:
1) Kalibracja widma jest wymagana przy każdym włączeniu komputera
2) Wykonuj kalibrację celownika co miesiąc
3) Kalibrację złota i niklu należy wykonywać przynajmniej raz w tygodniu
4) Podczas pomiaru należy wybrać plik testowy w zależności od stali zastosowanej w wyrobie.
5) Dla nowych produktów, które nie posiadają pliku testowego należy utworzyć plik testowy.
3. Znaczenie plików testowych:
Przykład: Au-Ni-Cu (100-221 sn 4%@0,2 cfp
Au-Ni-Cu —— Sprawdź grubość niklowania, a następnie złocenia na podłożu miedzianym.
(100-221 sn 4% ——- AMP numer materiału miedzi miedź zawierająca 4% cyny)

2. Kontrola wyrobów galwanicznych – kontrola przyczepności
Kontrola przyczepności jest niezbędnym elementem kontroli wyrobów galwanicznych. Słaba przyczepność jest najczęstszą wadą podczas kontroli produktów galwanicznych. Zwykle istnieją dwie metody kontroli:
1. Metoda gięcia: Najpierw użyj blachy miedzianej o tej samej grubości, co wymagana końcówka detekcyjna, aby wyłożyć obszar, który ma zostać zgięty, za pomocą szczypiec płaskich zgnij próbkę do 180 stopni i użyj mikroskopu, aby sprawdzić, czy jest łuszczenie się lub łuszczenie się powłoki na zgiętej powierzchni.
2. Metoda z użyciem taśmy: Użyj taśmy 3M, aby mocno przykleić się do powierzchni badanej próbki, pionowo pod kątem 90 stopni, szybko oderwij taśmę i obserwuj odrywanie się folii metalowej na taśmie. Jeśli nie możesz obserwować wyraźnie oczami, możesz do obserwacji użyć mikroskopu o powiększeniu 10x.
3. Ustalenie wyniku:
a) Nie powinno dochodzić do opadania proszku metalicznego ani przyklejania się taśmy klejącej.
b) Powłoka metalowa nie powinna się odklejać.
c) Dopóki materiał podstawowy nie jest uszkodzony, po zgięciu nie powinno być żadnych poważnych pęknięć ani łuszczenia.
d) Nie powinno być żadnych pęcherzyków.
e) Nie powinno być odsłonięcia metalu pod spodem bez uszkodzenia materiału podstawowego.
4. Gdy przyczepność jest słaba, należy nauczyć się rozróżniać położenie złuszczonej warstwy. Za pomocą mikroskopu i promieni rentgenowskich można sprawdzić grubość złuszczonej powłoki, aby określić, na którym stanowisku pracy występuje problem.
3. Kontrola wyrobów galwanicznych – kontrola lutowalności
1. Lutowalność jest podstawową funkcją i celem cynowania i cynowania. Jeśli istnieją wymagania dotyczące procesu po lutowaniu, słabe spawanie jest poważną wadą.
2.Podstawowe metody badania lutu:
1) Metoda bezpośredniego zanurzenia w cynie: Zgodnie z rysunkami należy bezpośrednio zanurzyć część lutowniczą w wymaganym topniku i zanurzyć ją w piecu do cyny o temperaturze 235 stopni. Po 5 sekundach należy go powoli wyjąć z prędkością około 25 MM/S. Po wyjęciu ostudź do normalnej temperatury i użyj mikroskopu 10x, aby obserwować i ocenić: powierzchnia ocynowana powinna być większa niż 95%, ocynowana powierzchnia powinna być gładka i czysta, nie ma na niej odrzutów lutowia, wylutowań, porów i innymi zjawiskami, co oznacza, że jest kwalifikowany.
2) Najpierw starzenie, a następnie spawanie. W przypadku produktów o specjalnych wymaganiach dotyczących niektórych powierzchni działających pod wpływem sił, próbki należy poddać starzeniu przez 8 lub 16 godzin przy użyciu maszyny do badania starzenia parowego przed testem spawania w celu określenia wydajności produktu w trudnych warunkach użytkowania. Wydajność spawania.
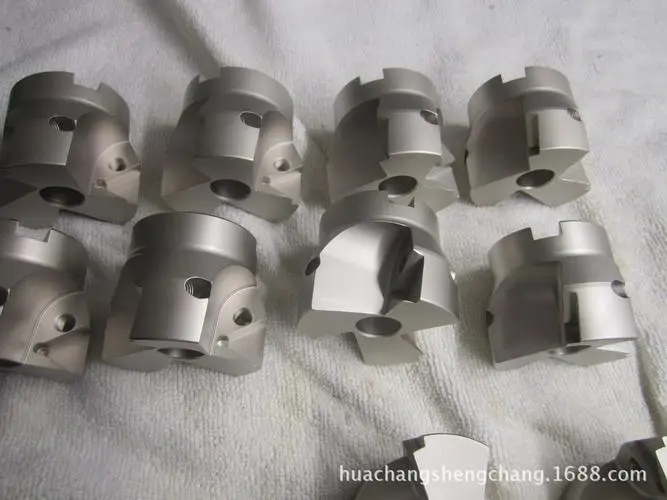
4. Kontrola wyrobów galwanicznych – kontrola wyglądu
1. Kontrola wyglądu jest podstawowym elementem kontroli galwanizacji. Już na pierwszy rzut oka widać przydatność warunków procesu galwanicznego i możliwe zmiany w roztworze galwanicznym. Różni klienci mają różne wymagania dotyczące wyglądu. Wszystkie końcówki galwaniczne należy obserwować pod mikroskopem co najmniej 10 razy większym. W przypadku usterek, które wystąpiły, im większe powiększenie, tym bardziej pomocna jest analiza przyczyny problemu.
2. Etapy kontroli:
1). Pobrać próbkę, umieścić ją pod mikroskopem o powiększeniu 10x i oświetlić pionowo standardowym źródłem białego światła:
2). Obserwuj stan powierzchni produktu przez okular.
3. Sposób oceny:
1). Kolor powinien być jednolity, bez ciemnego lub jasnego koloru lub mieć różne kolory (takie jak czernienie, zaczerwienienie lub żółknięcie). Pozłacanie nie powinno powodować poważnych różnic w kolorze.
2). Nie pozwól, aby przykleiły się do niego ciała obce (płatki włosów, kurz, olej, kryształki).
3). Musi być suche i nie może być zabrudzone wilgocią.
4). Dobra gładkość, brak dziur i cząstek.
5). Nie powinno być żadnych nacisków, zarysowań, zadrapań i innych zjawisk deformacyjnych oraz uszkodzeń platerowanych części.
6). Dolna warstwa nie może być odsłonięta. Jeśli chodzi o wygląd cyny i ołowiu, dopuszczalne jest kilka (nie więcej niż 5%) wżerów i wżerów, o ile nie wpływa to na lutowność.
7). Powłoka nie może wykazywać pęcherzy, łuszczenia się lub innej słabej przyczepności.
8). Stanowisko galwaniczne należy wykonać zgodnie z rysunkami. Inżynier ds. kontroli jakości może podjąć decyzję o odpowiednim złagodzeniu standardu bez wpływu na funkcję.
9). W przypadku podejrzanych wad wyglądu inżynier QE powinien ustawić próbkę graniczną i pomocnicze standardy wyglądu.
5. Kontrola wyrobów galwanicznych – kontrola opakowań
Kontrola opakowań produktów galwanicznych wymaga, aby kierunek pakowania był prawidłowy, tacki i pudełka do pakowania były czyste i uporządkowane oraz nie były uszkodzone: etykiety były kompletne i prawidłowe, a liczba etykiet wewnętrznych i zewnętrznych była zgodna.
6. Kontrola wyrobów galwanicznych – próba w mgle solnej
Po przejściu testu mgły solnej powierzchnia niekwalifikowanych części galwanicznych stanie się czarna i rozwinie się czerwona rdza. Oczywiście różne rodzaje galwanizacji dadzą różne wyniki.
Test mgły solnej produktów galwanicznych dzieli się na dwie kategorie: jedna to test narażenia na środowisko naturalne; drugi to sztuczny, przyspieszony test w symulowanym środowisku mgły solnej. Test sztucznego symulowanego środowiska mgły solnej polega na użyciu sprzętu testowego o określonej przestrzeni objętościowej – komorze testowej mgły solnej, w celu zastosowania sztucznych metod w jej przestrzeni objętościowej w celu wytworzenia środowiska mgły solnej w celu oceny odporności na korozję w mgle solnej i jakości produkt. .
Testy sztucznej symulowanej mgły solnej obejmują:
1) Test neutralnej mgły solnej (test NSS) jest najwcześniejszą metodą przyspieszonego badania korozji o najszerszym zakresie zastosowań. Wykorzystuje 5% roztwór soli chlorku sodu, a wartość pH roztworu dostosowuje się do zakresu neutralnego (6 do 7) jako roztwór do opryskiwania. Temperatura badania wynosi 35 ℃, a szybkość sedymentacji mgły solnej musi wynosić 1 ~ 2 ml/80 cm3.h.
2) Test octanowej mgły solnej (test ASS) opracowano na podstawie testu obojętnej mgły solnej. Dodaje trochę lodowatego kwasu octowego do 5% roztworu chlorku sodu, aby obniżyć wartość pH roztworu do około 3, powodując, że roztwór jest kwaśny, a powstała mgła solna również zmienia się z obojętnej mgły solnej na kwaśną. Szybkość korozji jest około 3 razy większa niż w teście NSS.
3) Test w mgle solnej z przyspieszoną solą miedzi (test CASS) to szybki test korozji w mgle solnej opracowany niedawno za granicą. Temperatura testu wynosi 50°C. Do roztworu soli dodaje się niewielką ilość soli miedzi i chlorku miedzi, aby silnie wywołać korozję. Szybkość korozji jest około 8 razy większa niż w teście NSS.
Powyższe obejmują standardy kontroli i metody kontroli produktów galwanizowanych, w tym kontrolę grubości powłoki produktu galwanicznego, kontrolę przyczepności, kontrolę spawalności, kontrolę wyglądu, kontrolę opakowania, test mgły solnej,
Czas publikacji: 05 czerwca 2024 r