Проверка гальванических оконечных изделий является незаменимой задачей после завершения гальваники. Только гальванические изделия, прошедшие контроль, могут быть переданы на следующий процесс для использования.
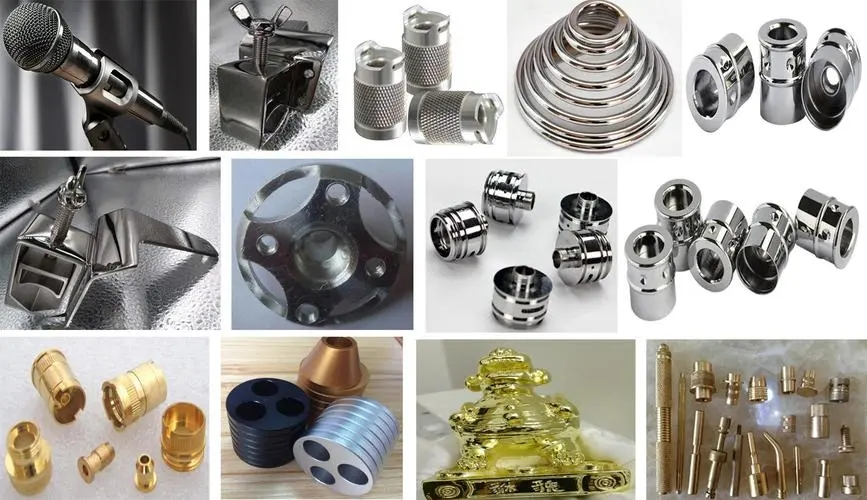
Обычно объектами проверки гальванических изделий являются: толщина пленки, адгезия, способность к пайке, внешний вид, упаковка и испытание в солевом тумане. Для изделий с особыми требованиями к чертежам проводятся испытания на пористость (30U”) по золоту методом паров азотной кислоты, изделий из никеля с палладиевым покрытием (методом гель-электролиза) или другие экологические испытания.
1. Проверка гальванических изделий – проверка толщины пленки.
1. Толщина пленки является основным параметром контроля гальваники. Основным используемым инструментом является флуоресцентный измеритель толщины пленки (РЕНТГЕНОВСКИЙ). Принцип заключается в использовании рентгеновских лучей для облучения покрытия, сбора энергетического спектра, возвращаемого покрытием, и определения толщины и состава покрытия.
2. Меры предосторожности при использовании РЕНТГЕНОВСКОГО ИЗЛУЧЕНИЯ:
1) Калибровка спектра необходима при каждом включении компьютера
2) Делайте калибровку прицела каждый месяц.
3) Калибровку золото-никель следует проводить не реже одного раза в неделю.
4) При измерении тестовый файл следует выбирать в соответствии со сталью, используемой в изделии.
5) Для новых продуктов, у которых нет тестового файла, необходимо создать тестовый файл.
3. Значение тестовых файлов:
Пример: Au-Ni-Cu(100-221 sn 4% при 0,2 cfp
Au-Ni-Cu —— Проверьте толщину никелирования, а затем позолоты на медной подложке.
(100-221 sn 4%——-AMP номер медного материала медь, содержащая 4% олова)

2. Проверка гальванических изделий и проверка адгезии.
Проверка адгезии является необходимым элементом проверки гальванических изделий. Плохая адгезия является наиболее распространенным дефектом при контроле гальванических изделий. Обычно существует два метода проверки:
1. Метод изгиба: сначала используйте медный лист той же толщины, что и требуемый терминал обнаружения, чтобы заполнить область, подлежащую изгибу, используйте плоскогубцы, чтобы согнуть образец на 180 градусов, и используйте микроскоп, чтобы наблюдать, есть ли отслаивание или отслаивание покрытия на гнутой поверхности.
2. Метод ленты: используйте ленту 3M, чтобы прочно приклеить ее к поверхности испытуемого образца вертикально под углом 90 градусов, быстро оторвите ленту и наблюдайте, как металлическая пленка отслаивается на ленте. Если вы не можете четко наблюдать глазами, вы можете использовать для наблюдения микроскоп с 10-кратным увеличением.
3. Определение результата:
а) Не должно быть попадания металлического порошка или прилипания заплаточной ленты.
б) Металлическое покрытие не должно отслаиваться.
в) Если основной материал не сломан, после изгиба не должно быть серьезных трещин или отслоений.
г) Не должно быть пузырей.
д) Не должно быть обнажения основного металла без разрушения основного материала.
4. При плохой адгезии следует научиться различать место отслаивания слоя. Вы можете использовать микроскоп и рентген, чтобы проверить толщину отслоившегося покрытия и определить, на какой рабочей станции возникла проблема.
3. Проверка гальванической продукции и проверка паяемости.
1. Паяемость является основной функцией и целью лужения и лужения. Если есть требования к процессу после пайки, плохая сварка является серьезным дефектом.
2.Основные методы тестирования припоя:
1) Метод прямого погружения в олово: в соответствии с чертежами непосредственно погрузите припой в необходимый флюс и погрузите его в оловянную печь с температурой 235 градусов. Через 5 секунд его следует медленно вынуть со скоростью около 25 мм/с. После извлечения охладите его до нормальной температуры и используйте 10-кратный микроскоп, чтобы наблюдать и судить: площадь лужения должна быть больше 95%, луженая область должна быть гладкой и чистой, не должно быть отторжений припоя, распайки, точечных отверстий и другие явления, а значит, квалифицированы.
2)Сначала старение, а затем сварка. Для продуктов с особыми требованиями к некоторым силовым поверхностям образцы должны быть выдержаны в течение 8 или 16 часов с использованием машины для испытания на старение паром перед испытанием на сварку, чтобы определить характеристики продукта в суровых условиях эксплуатации. Сварочные характеристики.
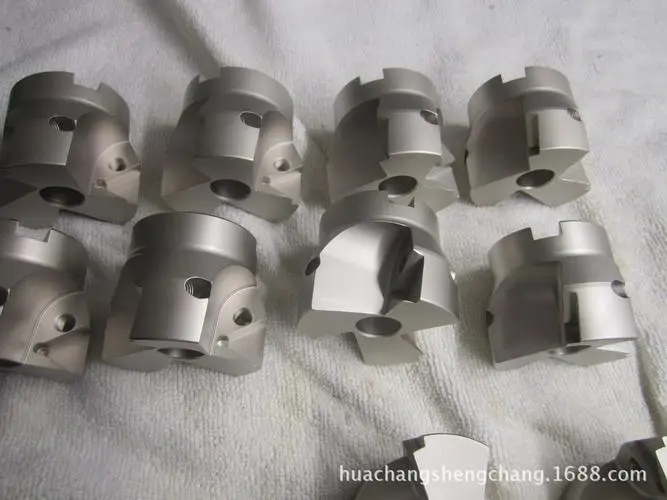
4. Проверка внешнего вида гальванической продукции.
1. Проверка внешнего вида является основным элементом проверки гальваники. По внешнему виду видно соответствие условий процесса гальванотехники и возможные изменения в гальваническом растворе. У разных клиентов разные требования к внешнему виду. Все гальванические выводы следует рассматривать под микроскопом не менее чем в 10 раз больше. Чем больше увеличение для возникших дефектов, тем полезнее проанализировать причину проблемы.
2. Этапы проверки:
1). Возьмите образец, поместите его под 10-кратный микроскоп и осветите его вертикально стандартным источником белого света:
2). Наблюдайте за состоянием поверхности изделия через окуляр.
3. Метод решения:
1). Цвет должен быть однородным, без темных или светлых оттенков, а также с различными оттенками (например, почернением, покраснением или пожелтением). При золотом покрытии не должно быть серьезной разницы в цвете.
2). Не допускайте прилипания к нему посторонних предметов (волос, пыли, масла, кристаллов).
3). Он должен быть сухим и не иметь пятен от влаги.
4). Хорошая гладкость, без дырок и частиц.
5). На плакированных деталях не должно быть давления, царапин, царапин и других деформационных явлений, а также повреждений.
6). Нижний слой не должен быть обнажен. Что касается появления олово-свинца, то допускается наличие нескольких (не более 5%) ямок и ямок, если это не влияет на паяемость.
7). Покрытие не должно иметь вздутий, отслоений или других проблем с адгезией.
8). Положение гальванического покрытия должно выполняться в соответствии с чертежами. Инженер по обеспечению качества может принять решение ослабить стандарт соответствующим образом, не влияя на функцию.
9). При подозрительных дефектах внешнего вида инженер по контролю качества должен установить предельную выборку и вспомогательные стандарты внешнего вида.
5. Проверка упаковки гальванической продукции.
Проверка упаковки гальванической продукции требует, чтобы направление упаковки было правильным, упаковочные лотки и коробки были чистыми и опрятными, не было повреждений: этикетки были заполнены и правильны, а количество внутренних и внешних этикеток было одинаковым.
6. Проверка гальванического изделия - испытание на солевой туман.
После прохождения испытания в солевом тумане поверхность неквалифицированных гальванических деталей почернеет и на них появится красная ржавчина. Конечно, разные виды гальваники дадут разные результаты.
Испытание гальванических изделий в солевом тумане делится на две категории: испытание на воздействие окружающей среды; другой - это испытание на искусственную ускоренную имитацию соляного тумана. Испытание на искусственную среду солевого тумана заключается в использовании испытательного оборудования с определенным объемом пространства - испытательной камеры с солевым туманом, с использованием искусственных методов в ее объемном пространстве для создания среды солевого тумана для оценки характеристик устойчивости к коррозии в солевом тумане и качества продукт. .
Испытания на искусственный солевой туман включают в себя:
1) Испытание нейтральным солевым туманом (испытание NSS) — это самый ранний метод испытаний на ускоренную коррозию, имеющий самую широкую область применения. В нем используется 5% раствор соли хлорида натрия, а значение pH раствора доводится до нейтрального диапазона (от 6 до 7) при распылении раствора. Температура испытания составляет 35 ℃, а скорость осаждения солевого тумана должна находиться в пределах 1–2 мл/80 см?.ч.
2) Испытание в ацетатно-солевом тумане (ASS-тест) разработано на основе испытания в нейтральном солевом тумане. Он добавляет немного ледяной уксусной кислоты к 5% раствору хлорида натрия, чтобы снизить значение pH раствора примерно до 3, делая раствор кислым, и образующийся в результате соляной туман также меняется с нейтрального солевого тумана на кислый. Его скорость коррозии примерно в 3 раза выше, чем в тесте NSS.
3) Испытание на ускоренный ацетат солевого тумана с медной солью (тест CASS) представляет собой быстрое испытание на коррозию в солевом тумане, недавно разработанное за рубежом. Температура испытания составляет 50°C. К раствору соли добавляют небольшое количество соли меди и хлорида меди, чтобы вызвать коррозию. Скорость коррозии примерно в 8 раз выше, чем в тесте NSS.
Выше приведены стандарты контроля и методы контроля гальванических изделий, включая проверку толщины пленки гальванического изделия, проверку адгезии, проверку свариваемости, проверку внешнего вида, проверку упаковки, испытание в солевом тумане,
Время публикации: 05 июня 2024 г.