Kontrola galvanizovaných koncových produktov je nevyhnutnou úlohou po dokončení galvanizácie. Iba galvanicky pokovované výrobky, ktoré prejdú kontrolou, môžu byť odovzdané do ďalšieho procesu na použitie.
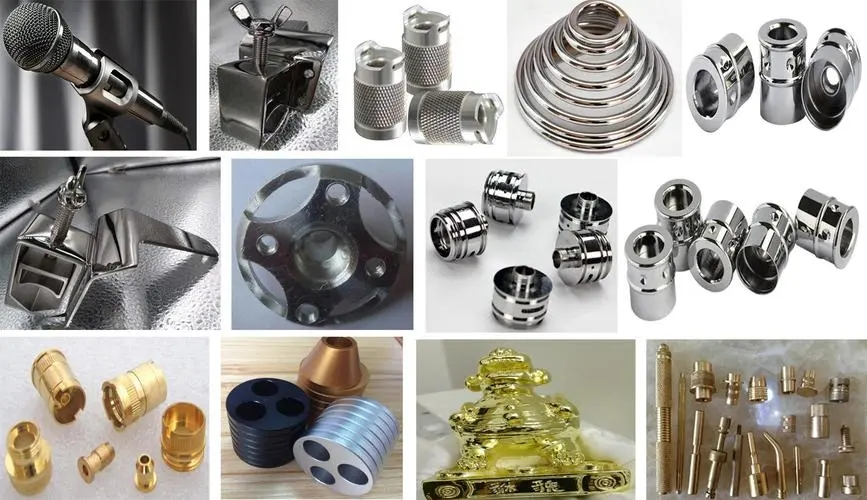
Zvyčajne sú kontrolnými položkami pre galvanizované výrobky: hrúbka filmu, priľnavosť, schopnosť spájkovania, vzhľad, balenie a test soľným sprejom. Pre produkty so špeciálnymi požiadavkami na výkresy existujú testy pórovitosti (30U”) pre zlato pomocou metódy pár kyseliny dusičnej, produkty z paládiom pokovovaného niklu (s použitím metódy gélovej elektrolýzy) alebo iné environmentálne testy.
1. Kontrola galvanického produktu - kontrola hrúbky filmu
1. Hrúbka filmu je základnou položkou pre kontrolu galvanického pokovovania. Základným používaným nástrojom je fluorescenčný merač hrúbky filmu (X-RAY). Princípom je použitie röntgenového žiarenia na ožarovanie povlaku, zber energetického spektra vráteného povlakom a identifikáciu hrúbky a zloženia povlaku.
2. Bezpečnostné opatrenia pri používaní RTG:
1) Kalibrácia spektra sa vyžaduje pri každom zapnutí počítača
2) Vykonajte kalibráciu zameriavacieho kríža každý mesiac
3) Zlato-niklová kalibrácia by sa mala vykonávať aspoň raz týždenne
4) Pri meraní by sa mal skúšobný súbor zvoliť podľa ocele použitej vo výrobku.
5) Pre nové produkty, ktoré nemajú testovací súbor, by mal byť vytvorený testovací súbor.
3. Význam testovacích súborov:
Príklad: Au-Ni-Cu(100-221 sn 4%@0,2 cfp
Au-Ni-Cu——Otestujte hrúbku poniklovania a potom zlatenie na medenom substráte.
(100-221 sn 4%——-AMP číslo materiálu medi medi s obsahom 4% cínu)

2. Kontrola galvanického produktu-kontrola priľnavosti
Kontrola priľnavosti je nevyhnutnou kontrolnou položkou pri galvanickom pokovovaní výrobkov. Zlá priľnavosť je najčastejšou chybou pri kontrole galvanického pokovovania. Zvyčajne existujú dva spôsoby kontroly:
1. Metóda ohýbania: Najprv použite medený plech s rovnakou hrúbkou ako je požadovaná detekčná koncovka na podloženie oblasti, ktorá sa má ohýbať, použite ploché kliešte na ohnutie vzorky o 180 stupňov a pomocou mikroskopu pozorujte, či je odlupovanie alebo odlupovanie povlaku na ohnutom povrchu.
2. Metóda pásky: Použite 3M pásku na pevné prilepenie na povrch vzorky, ktorá sa má testovať, vertikálne pod uhlom 90 stupňov, rýchlo odtrhnite pásku a pozorujte, ako sa kovový film na páske odlupuje. Ak nemôžete jasne pozorovať očami, môžete na pozorovanie použiť 10x mikroskop.
3. Určenie výsledku:
a) Nemalo by dochádzať k vypadávaniu kovového prášku alebo lepeniu lepiacej pásky.
b) Kovový povlak by sa nemal odlupovať.
c) Pokiaľ základný materiál nie je zlomený, po ohnutí by nemalo dôjsť k vážnemu praskaniu alebo odlupovaniu.
d) Nemalo by tam byť žiadne bublanie.
e) Nemalo by dôjsť k žiadnemu odkrytiu podkladového kovu bez toho, aby nedošlo k porušeniu základného materiálu.
4. Keď je priľnavosť slabá, mali by ste sa naučiť rozlišovať miesto odlúpnutej vrstvy. Pomocou mikroskopu a röntgenového žiarenia môžete otestovať hrúbku odlúpnutého povlaku a určiť pracovnú stanicu s problémom.
3. Kontrola galvanického produktu-kontrola spájkovateľnosti
1.Spájkovateľnosť je základnou funkciou a účelom pocínovania a cínovania. Ak existujú požiadavky na proces po spájkovaní, zlé zváranie je vážnou chybou.
2. Základné metódy testovania spájkovania:
1) Metóda priameho ponorenia cínu: Podľa nákresov priamo ponorte spájkovaný diel do požadovaného taviva a ponorte ho do 235-stupňovej cínovej pece. Po 5 sekundách by sa malo pomaly vybrať rýchlosťou približne 25 mm/s. Po vybratí ochlaďte na normálnu teplotu a pomocou 10-násobného mikroskopu pozorujte a posúďte: pocínovaná plocha by mala byť väčšia ako 95 %, pocínovaná plocha by mala byť hladká a čistá, nedochádza k odmietnutiu spájky, odspájkovaniu, dierkam a iné javy, čo znamená, že je kvalifikovaný.
2) Najprv starnutie a potom zváranie. V prípade produktov so špeciálnymi požiadavkami na niektoré silové povrchy by sa vzorky mali nechať zrieť 8 alebo 16 hodín pomocou zariadenia na testovanie starnutia parou pred testom zvárania, aby sa určil výkon produktu v drsnom prostredí. Výkon zvárania.
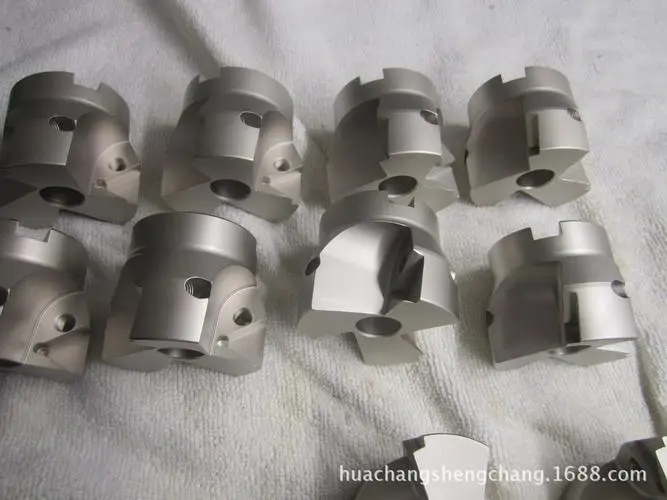
4. Kontrola galvanického produktu-kontrola vzhľadu
1.Kontrola vzhľadu je základnou kontrolnou položkou kontroly galvanického pokovovania. Podľa vzhľadu vidíme vhodnosť podmienok procesu galvanizácie a možné zmeny v roztoku galvanizácie. Rôzni zákazníci majú rôzne požiadavky na vzhľad. Všetky galvanicky pokovené svorky by sa mali pozorovať mikroskopom aspoň 10-krát väčším. V prípade defektov, ktoré sa vyskytli, platí, že čím väčšie zväčšenie, tým užitočnejšie je analyzovať príčinu problému.
2. Kroky kontroly:
1). Vezmite vzorku a umiestnite ju pod 10x mikroskop a osvetlite ju vertikálne štandardným zdrojom bieleho svetla:
2). Cez okulár sledujte stav povrchu výrobku.
3. Metóda posudzovania:
1). Farba by mala byť jednotná, bez akejkoľvek tmavej alebo svetlej farby alebo s rôznymi farbami (ako je sčernenie, začervenanie alebo zožltnutie). V pozlátení by nemal byť žiadny vážny farebný rozdiel.
2). Nedovoľte, aby sa na ňom prilepili žiadne cudzie látky (vlasové vločky, prach, olej, kryštály).
3). Musí byť suchý a nesmie byť znečistený vlhkosťou.
4). Dobrá hladkosť, žiadne diery alebo častice.
5). Nemalo by dochádzať k tlaku, škrabancom, škrabancom a iným deformačným javom, ako aj poškodeniu pokovovaných častí.
6). Spodná vrstva nesmie byť odkrytá. Pokiaľ ide o vzhľad cínu a olova, je povolených niekoľko (nie viac ako 5%) jamiek a jamiek, pokiaľ to neovplyvňuje spájkovateľnosť.
7). Náter nesmie mať pľuzgiere, odlupovanie alebo inú slabú priľnavosť.
8). Pozícia galvanického pokovovania sa musí vykonať v súlade s výkresmi. Inžinier QE sa môže rozhodnúť primerane uvoľniť štandard bez ovplyvnenia funkcie.
9). Pre podozrivé chyby vzhľadu by mal inžinier QE nastaviť limitné vzorky a pomocné štandardy vzhľadu.
5. Kontrola galvanického produktu-kontrola balenia
Kontrola balenia galvanického produktu vyžaduje, aby bol smer balenia správny, baliace podnosy a škatule boli čisté a upratané a nedošlo k poškodeniu: štítky sú vyplnené a správne a počet vnútorných a vonkajších štítkov je konzistentný.
6.Kontrola galvanického produktu-test soľným sprejom
Po absolvovaní testu soľným postrekom povrch nekvalifikovaných galvanizovaných dielov sčernie a vytvorí červenú hrdzu. Samozrejme, rôzne typy elektrolytického pokovovania prinesú rôzne výsledky.
Skúška produktov na galvanické pokovovanie soľným postrekom je rozdelená do dvoch kategórií: jedna je skúška vystavenia prirodzenému prostrediu; druhý je test v umelom zrýchlenom simulovanom prostredí soľnej hmly. Skúška prostredia v umelom simulovanom prostredí soľnej hmly je použiť testovacie zariadenie s určitým objemovým priestorom - skúšobnú komoru soľnej hmly, použiť umelé metódy v jej objemovom priestore na vytvorenie prostredia soľnej hmly na posúdenie odolnosti a kvality korózie v soľnej hmle. výrobok. .
Umelé simulované testy soľného postreku zahŕňajú:
1) Test neutrálnym soľným sprejom (NSS test) je najskoršia zrýchlená metóda testovania korózie s najširším aplikačným poľom. Používa 5% roztok soli chloridu sodného a hodnota pH roztoku je upravená na neutrálny rozsah (6 až 7) ako rozprašovací roztok. Skúšobná teplota je 35 °C a rýchlosť sedimentácie soľného postreku musí byť medzi 1~2 ml/80 cm?.h.
2) Test acetátovým soľným postrekom (ASS test) je vyvinutý na základe testu neutrálneho soľného postreku. Pridá trochu ľadovej kyseliny octovej do 5% roztoku chloridu sodného, aby sa hodnota pH roztoku znížila na približne 3, čím sa roztok okyslí a výsledný soľný sprej sa tiež zmení z neutrálneho soľného spreja na kyslý. Rýchlosť korózie je asi 3-krát rýchlejšia ako pri teste NSS.
3) Test postrekom octanom zrýchleným soľou medi (CASS test) je rýchly test korózie soľným sprejom, ktorý bol nedávno vyvinutý v zahraničí. Skúšobná teplota je 50°C. Na silnú indukciu korózie sa do soľného roztoku pridáva malé množstvo soli medi-chloridu medi. Rýchlosť korózie je približne 8-krát vyššia ako pri teste NSS.
Vyššie uvedené sú kontrolné normy a kontrolné metódy pre galvanicky pokovované výrobky, vrátane kontroly hrúbky galvanizovaného produktu, kontroly priľnavosti, kontroly zvariteľnosti, kontroly vzhľadu, kontroly balenia, testu soľným postrekom,
Čas odoslania: 05.06.2024